- Animal Feed Machine
- Animal Feed Production Line
- Fish Feed and Pet Food Machine
- Fish Feed and Pet Food Production Line
- Soybean Meal Machine
- Feather Meal Machine
- Biomass Wood Pellet Machine
- Biomass Briquette Machine
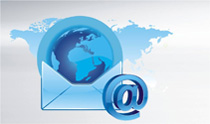
Email: carla@hnyearmega.com
Tel: +86 15093305912
Skype: zzhrsdcarlar
WhatsApp & WeChat: +86 15093305912
NEWS




Cleaning Tips of Feed Production Equipment
Equipment cleanup is a relatively troublesome thing for feed mills, especially for plants that are busy with production tasks. But if you ignore this issue, that will influence long-term quality stability.
In fact, almost all devices need to be cleaned after use for some time, some need to be cleaned outside, and some need to be cleaned both inside and outside. What we are talking about here is the part which can affect the quality of the product, mainly inside the equipment. In this article, based on the impact of equipment cleanup on the quality of products, the following cleaning suggestions are put forward, so as to help feed plant create a set of feed equipment cleaning solutions.
1. Mixer Cleaning
After a period of time, the inside of the mixer will be coated with a layer of material. If the content of grease is high, a thick layer of material will be accumulated in a shift. Some mixers are equipped with a liquid anti-mold nozzle in addition to the fuel injection device. Therefore, there are also residue on the mixer wall, paddle and the door.
Solution: Turn off power before cleaning. The cleaning person himself locks the knife switch and puts the key in his pocket. Then he can use special tool to scrap off the material cover on the inner wall, the nozzle, and the paddle. After that, open the door and clean it including the seal ring. Some mixers are relatively large and require people to enter before they can be cleaned. At this time, safety work is particularly important. In addition to being locked, special personnel are required to take care of it. The person who enters the mixer is responsible for opening the lock of the power box door.
Mixer cleaning frequency: 1-3 days per once
2. Granulation System Cleanup
The granulation system consists of a feed pellet machine, a cooler, a crusher and a grading screen. The parts requiring the most careful cleaning is the modulator and the granulation chamber. Since the modulator is difficult to open, the frequency of cleaning is generally not high. Some feed mills even only do once cleaning when it is broken down. The proper way is to clean up once every one or two weeks.
If the machine leaves unused for a long time, it should be cleaned to prevent the mildewing of the sticky feed. The pelletizing chamber should be cleaned thoroughly after the end of each shift. When adjust the feed pellet varieties, if they have the possibility of cross-contamination, you need to do cleaning before producing another kind. After the granulation and emptying the cooler, one person enters from the entrance hole and sweeps the residue from corners and the screen plate with wooden sticks or other tools. Finally, wipe the walls.
3. Cleaning of Permanent Magnets
The permanent magnet is for removing magnetic material such as iron. Iron filings not only have great effect on feed pellet, but also do harm to the equipment. It may also affect the passage of the feed, causing clogging. It is recommended that you clean up after each shift. The impurities removed from the permanent magnets are treated as waste.
4. Initial cleaning, finished product screening, grading screen cleaning
These three devices are all used for cleaning and grading, so they are easily blocked. In particular, the initial cleaning device is more easily when the amount of impurities is large. Usually after the end of each shift, open the above screens and remove the rope, impurities and hard blocks. The final result is to keep the inside of the screen clean and the screen mesh not blocked. The cleaned-up materials are processed according to actual conditions and some of them can be used.
5. Silo cleaning
Silo, including cylindrical steel silo, atrioventricular bulk silo, to-be-smashed silo, batching silo, to-be-granulated silo, finished product silo, buffer silo, etc., is a storage device for storing a certain amount of raw materials. All the above silos need to be cleaned. However, depending on the materials and frequency of use, the requirements for cleaning are different. Cylindrical steel silos, room silos, and bulk silos are generally used to store granular raw materials such as corn, wheat, and soybean meal. Before the new silo is used, it is necessary to enter the silo to sweep out the screw, cement blocks, mixed bars, etc. Do cleaning the space between the discharge and the scraper.
As for other silos, most of them are welded by steel plate and in shape of square, therefore there will be raw material in the corners, on the upper part of the cone and the upper part of the angle iron and rivets. The above silo shall be inspected frequently and emptied for cleaning when it is necessary. After emptying, it is recommended to use a compressed air machine bound with the bamboo rafts to blow off the scraps and then to clean the scraper or auger. Finally, use fresh raw materials to wash the warehouse.
6. Lift conveyor cleaning
Normally there will be some accumulation of materials on the base of the elevator. There are much more for self-cleaning elevator, much less on square base. It is recommended that corn and wheat elevator should be cleaned once every week and powder elevator should be cleaned once a day. If two or more kinds of raw material can’t be cross-contaminated, the lift should be cleaned once every time when the product is changed.
7. Feeder nose cleaning
At the end of the feeding process, the raw materials shall be cleaned, and all the materials shall enter the next process. The materials stuck to the feeding fence, the wall of the pipeline, and the inside of the bucket shall be cleaned at regular intervals. It is best to clean it once a day, at least once every 3 days.
In one words, almost all equipments need cleaning. However, actually many equipments have not been cleaned timely because of lack of proper arrangement, which leads to unstable product quality and continuous complaints. Therefore, companies must pay attention to this issue, make practical plan and do a good record.